The control system of our gypsum powder production line is designed and implemented by a team of highly skilled and experienced professionals. It is equipped with advanced technology and automation features that allow for precise monitoring and management of the entire production process. This ensures that the production line operates at its optimal capacity, resulting in high-quality gypsum powder with consistent properties.
One of the key advantages of the control system is its ability to regulate the various parameters involved in the production process, such as temperature, pressure, and flow rates. This level of control allows for the fine-tuning of the production parameters, which is essential for achieving the desired quality and consistency in the final product.
The control system is integrated with state-of-the-art sensors and monitoring devices that provide real-time data on the production process. This real-time data allows for immediate adjustments and interventions if any deviations or issues are detected, thereby minimizing the risk of production errors and ensuring the overall efficiency of the production line.
And the control system is also user-friendly, with a clear and intuitive interface that allows operators to easily monitor and manage the production process. This user-friendly design not only enhances the operational efficiency but also reduces the likelihood of human errors.
Users have manual control and DCS automatic control two ways to choose, the following focuses on the automatic control mode. The main calciner adopts the two-stage closed-loop control principle to keep the discharge temperature relatively stable. The system adopts the American FIX software for picture configuration, and consists of a DCS system controlled by PLC. The FIX control system displays the running state including two parts: analog quantity and switch quantity. The analog quantity displays the change of physical quantity digitally in time with the required engineering quantity on the corresponding equipment. The switch quantity displays the status of the device in various colors. The system includes four operation screens: the main screen of system flow, the interface of scale calibration, the interface of historical curve, the interface of report display and printing. In terms of program control, the material temperature is detected by PT100, calculated by PID, and the feeding speed is adjusted according to the set material temperature in time, and the set temperature is always maintained. The control system runs reliably, the failure rate is low, and the normal production is not affected. The system mainly consists of field control station (IO station), data communication system, man-machine interface unit (operator station OPS, engineer station ENS), cabinet, power supply and so on. The system has an open architecture and can provide multi-layer open data interface.
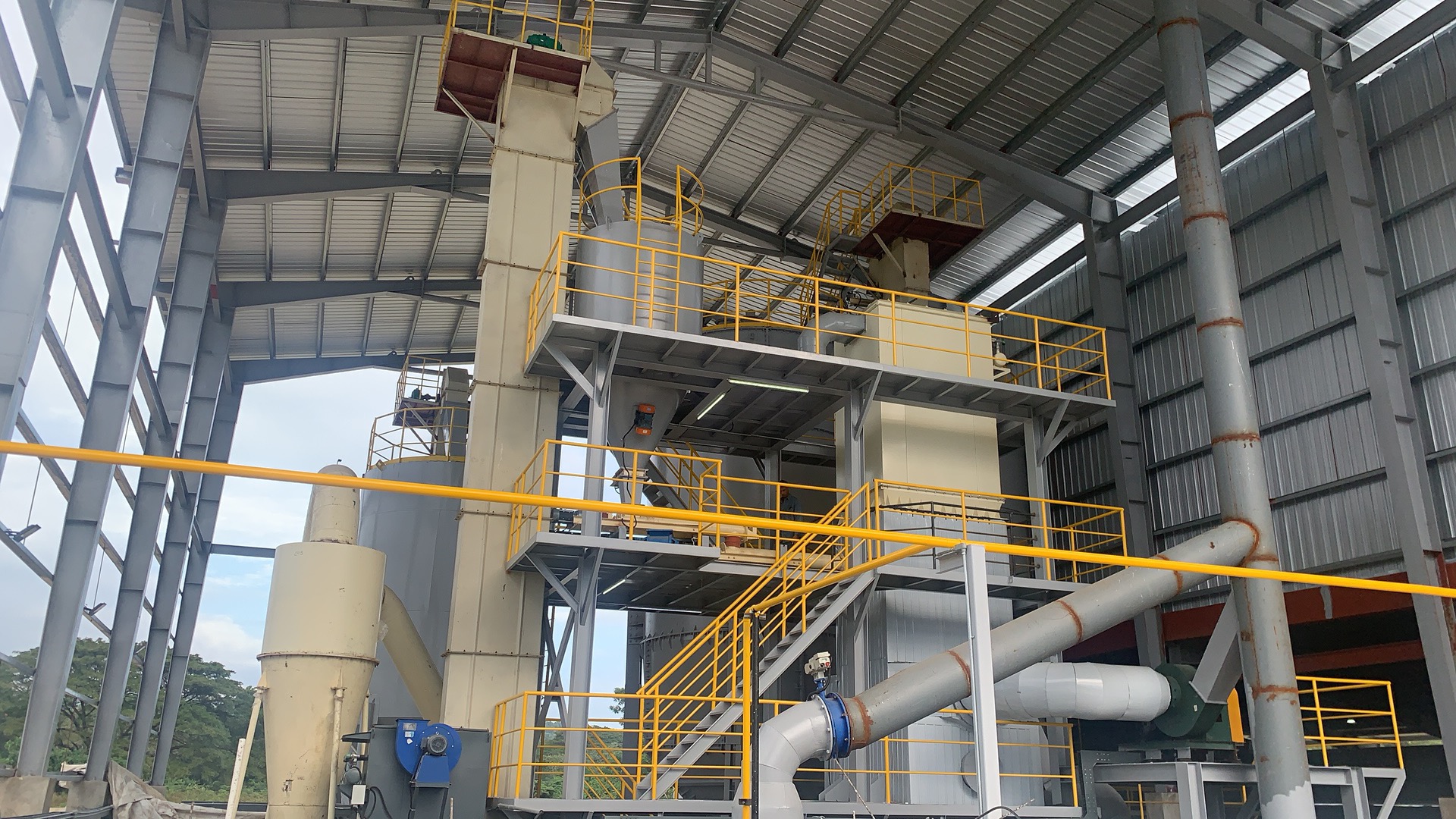
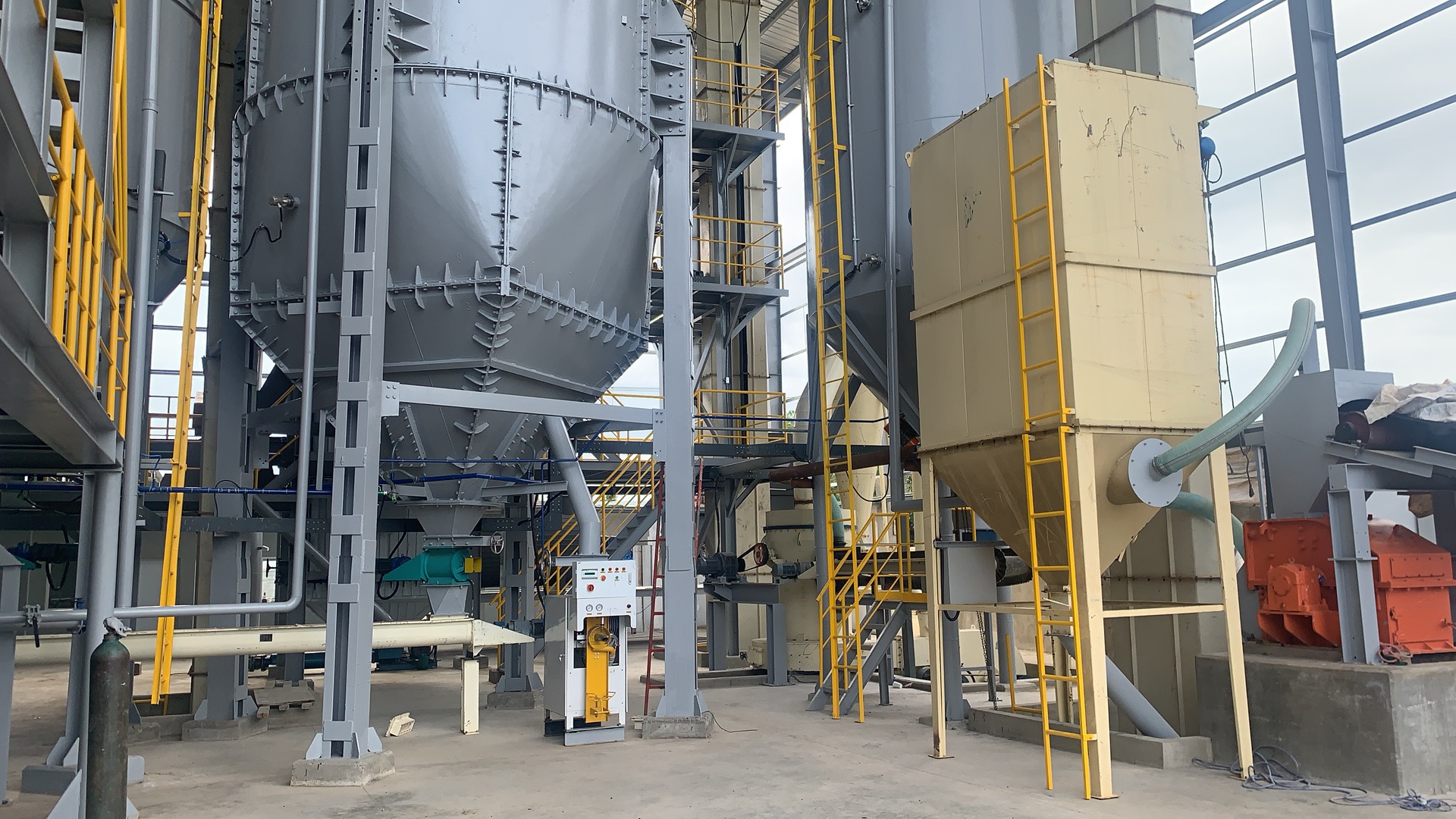
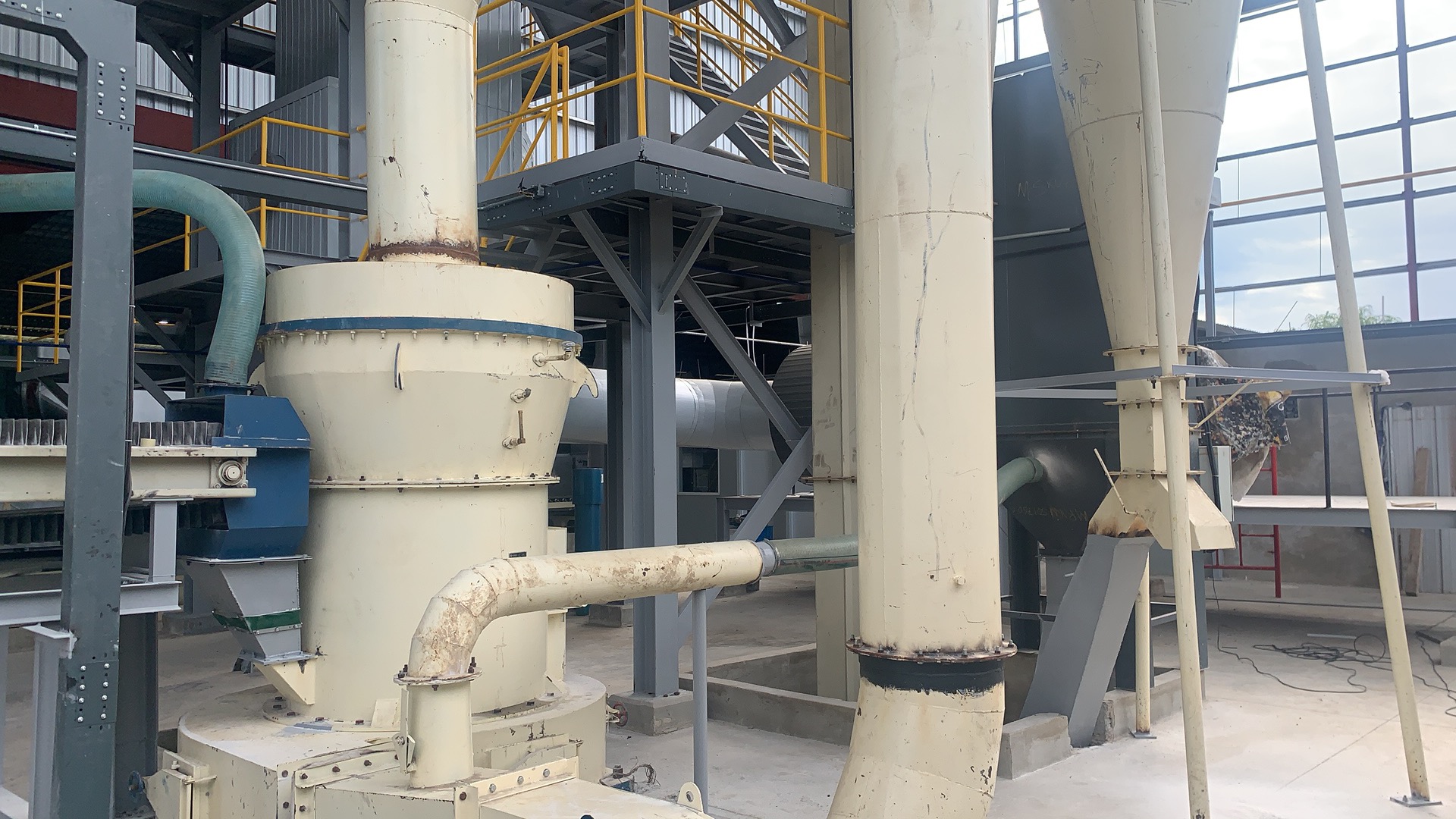
System features:
1.High reliability
Hardware redundancy design: no need for user programming, as long as the configuration can automatically realize several designs; Highly reliable I/0 module: spot separation, online spot replacement; Intelligent component design: Each piece is equipped with a microprocessor, supporting self-diagnosis, online maintenance and other functions; Intelligent conditioning technology: support analog universal input, maintenance-free adjustment; Electromagnetic compatibility design: anti-transient fast group pulse interference, RF interference suppression, low power design; Operation safety design: real-time data power down protection to ensure system information security; Manufacturing quality control: complete inspection process, comprehensive functional testing and comprehensive reliability test mechanism and other procedures, improve the "IS09001 quality Assurance System".
2. System opening
The whole side is open design, allowing users to function expansion and personality development; Configuration language according to IEC61131-3 standard; Modular system hardware, open software platform, professional application software.
3. Powerful
Support integrated development environment and offline and online programming, support global unified engineering real-time database; support on-line configuration and on-line debugging of control policies.
4.Easy maintenance
The I0 module is configured with industrial terminal group, the internal interconnection of the cabinet is standardized, so that "service starts from the terminal" support module, module network self-diagnosis, live plug and remove, online repair, easy maintenance: intelligent, easy maintenance, eliminate configuration waste, reduce spare parts; Remote technical support, timely and rapid system knowledge, training, maintenance services.
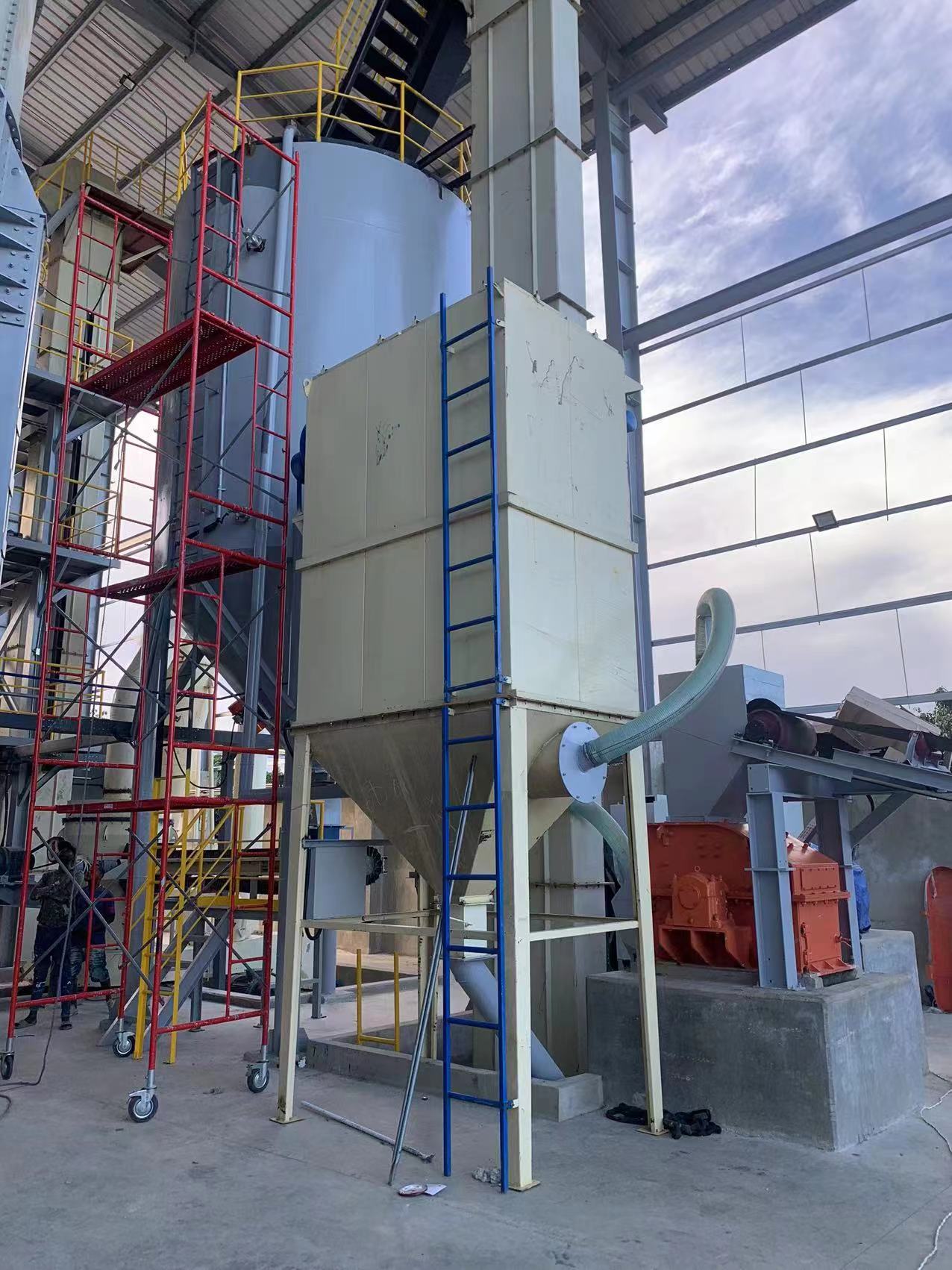
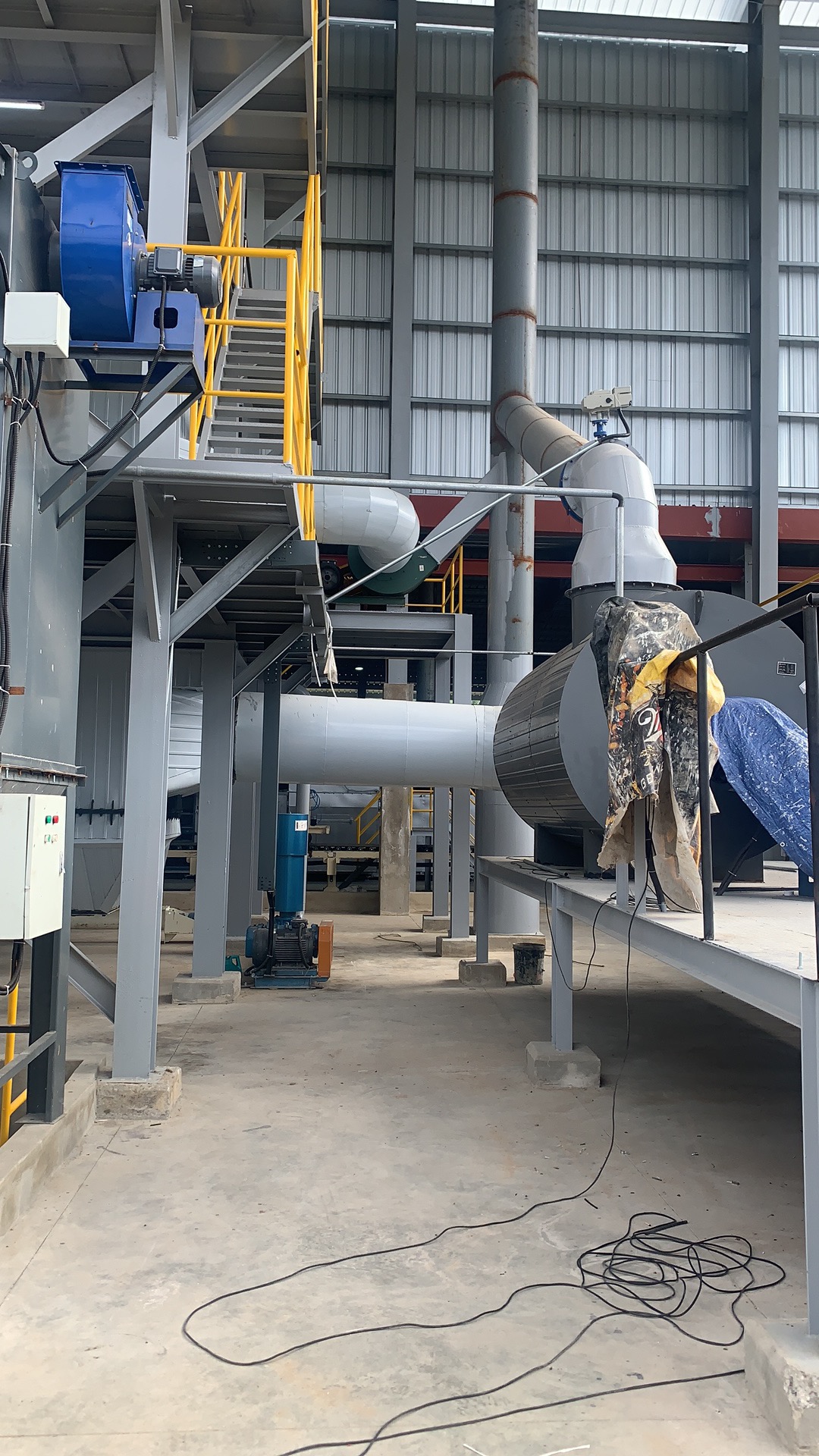
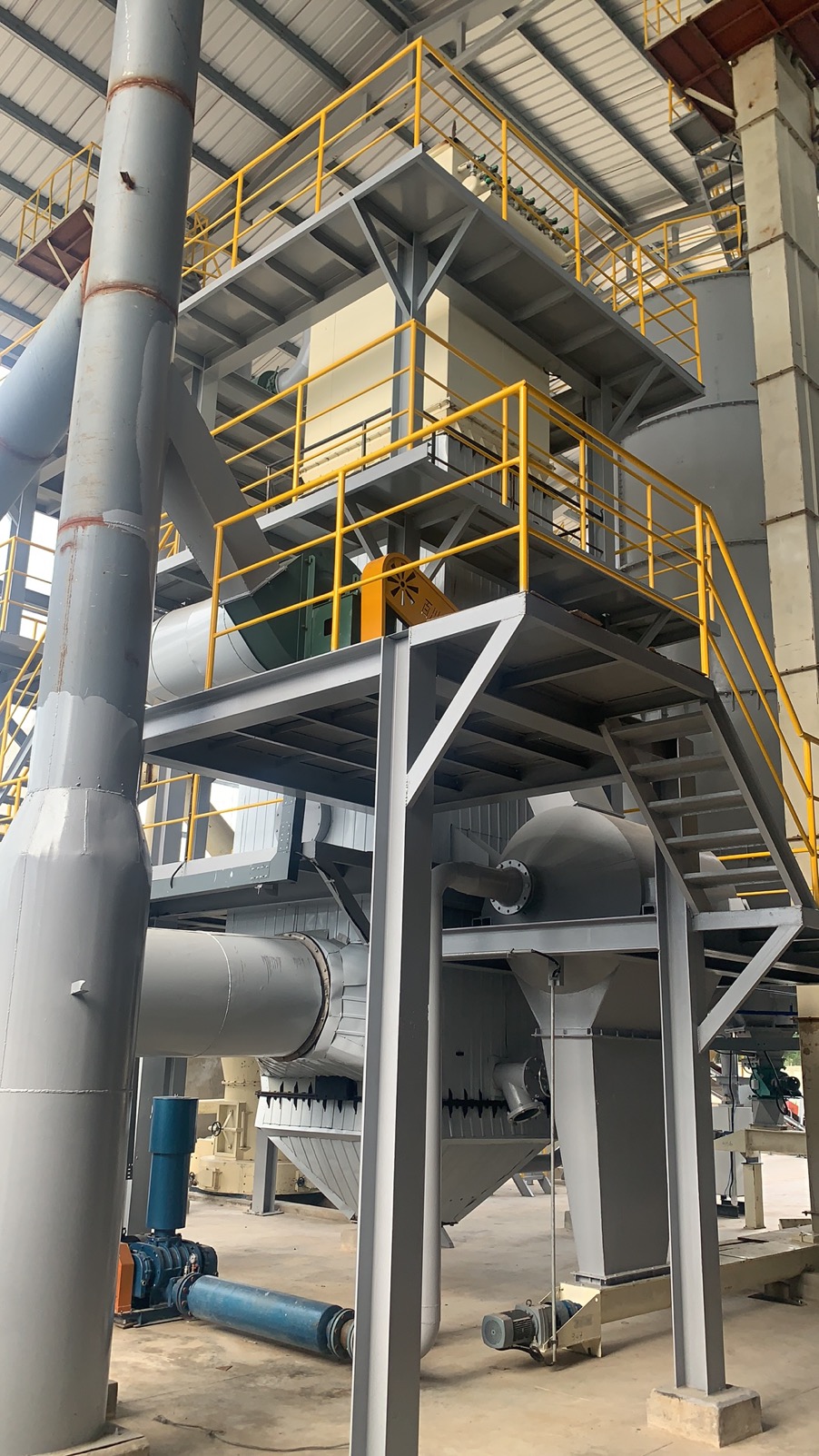
If you are in need of a gypsum powder production line, it is important to partner with a reputable and experienced supplier. A well-established supplier can provide you with a complete production line that is efficient, cost-effective, and tailored to your specific requirements. From raw material preparation to the final packaging of the gypsum powder, a reliable production line can streamline the entire process and ensure consistent quality output.
At our company, we specialize in providing comprehensive solutions for gypsum powder production. Our expertise in this field allows us to offer state-of-the-art production lines that are designed to maximize efficiency and productivity. Whether you are looking to set up a new production line or upgrade an existing one, we can work with you to develop a customized solution that meets your production needs.
Post time: Sep-09-2024