Introduction
The production of gypsum board, also known as drywall or plasterboard, involves several key processes, including the mixing of gypsum, water, and additives, as well as the forming, drying, and finishing of the boards. One critical aspect of the production line is the feeding system, which plays a crucial role in ensuring the efficient and continuous supply of raw materials to the various stages of the production process. In this article, we will explore the importance of a well-designed feeding system for gypsum board production lines and how it contributes to enhancing efficiency and quality.
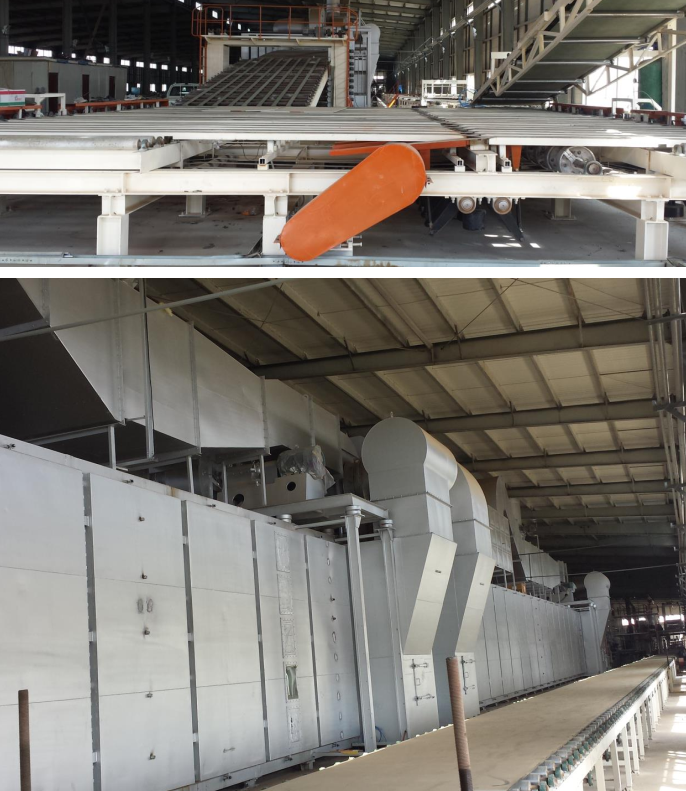
Importance of a Reliable Feeding System
A reliable feeding system is essential for the smooth operation of a gypsum board production line. It is responsible for delivering the raw materials, such as gypsum, water, and additives, to the mixer in a controlled and consistent manner. Any disruptions or inconsistencies in the feeding process can lead to variations in the composition of the gypsum slurry, which can ultimately affect the quality and performance of the finished boards. Therefore, investing in a high-quality feeding system is crucial for maintaining the integrity of the production process and ensuring the production of high-quality gypsum boards.
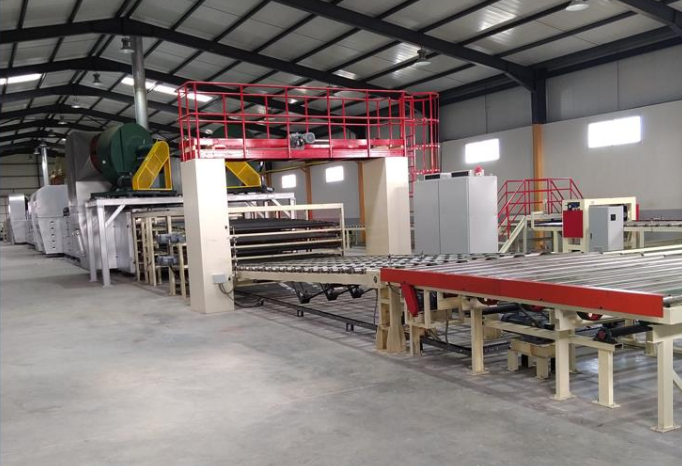
Key Considerations for Feeding System Design
When designing a feeding system for a gypsum board production line, several key considerations must be taken into account to ensure its effectiveness and reliability. These considerations include:
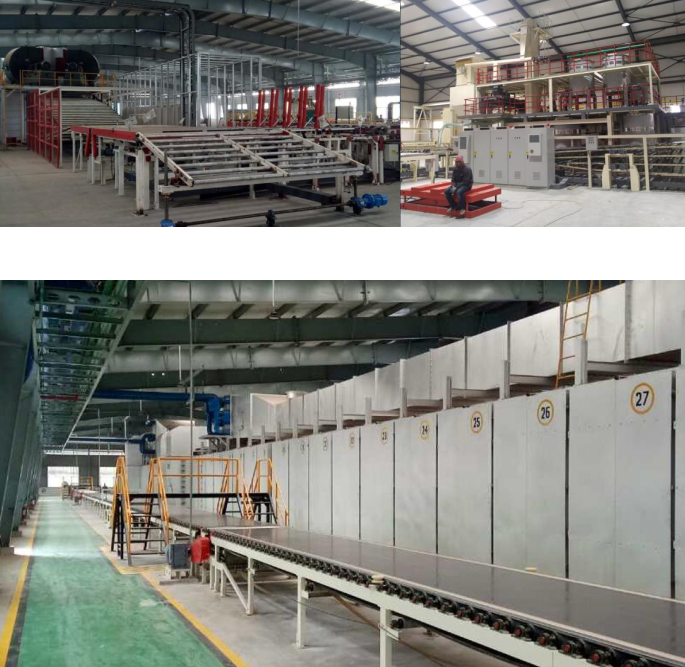
1. Material Handling: The feeding system must be capable of handling the various raw materials used in the production of gypsum boards, including gypsum, water, and additives. It should be designed to accommodate the specific characteristics of these materials, such as their flow properties, particle size, and bulk density.
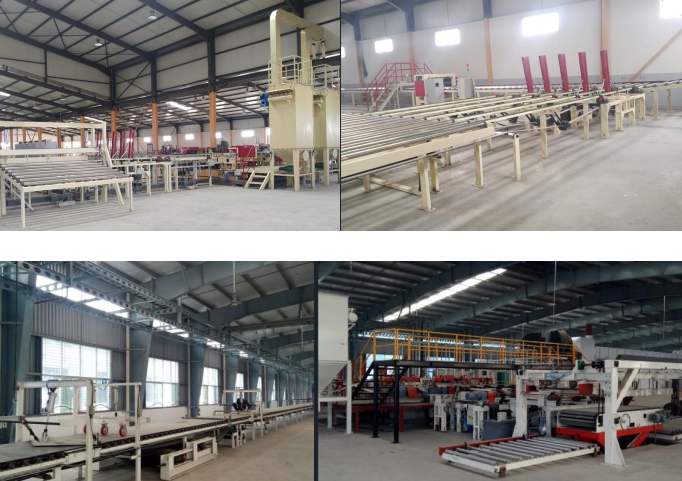
2. Precision and Control: The feeding system should provide precise and accurate control over the flow rate and proportion of each raw material being delivered to the mixer. This is essential for maintaining the desired composition of the gypsum slurry and achieving consistent board quality.
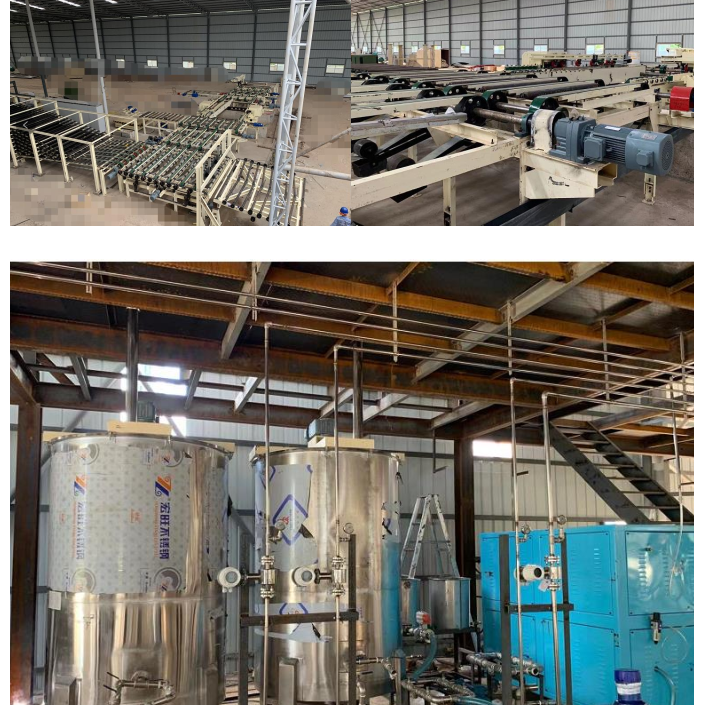
3. Flexibility: The feeding system should be flexible enough to accommodate changes in production requirements, such as variations in the recipe formulations or production rates. It should be capable of adjusting the feed rates and proportions of the raw materials to meet the specific demands of the production process.
4. Reliability and Maintenance: The feeding system should be designed for reliability and ease of maintenance to minimize downtime and ensure continuous operation. This includes the use of durable components, easy access for cleaning and inspection, and proactive maintenance practices.
Types of Feeding Systems
There are several types of feeding systems that can be used in gypsum board production lines, each with its own advantages and considerations. Some of the common feeding systems include:
1. Screw Feeders: Screw feeders are widely used for the controlled delivery of powdered or granular materials, such as gypsum and additives. They offer precise metering and can be designed with variable speed drives to adjust the feed rates as needed.
2. Belt Feeders: Belt feeders are suitable for handling bulk materials with varying flow properties. They are often used for the continuous and uniform feeding of gypsum and other materials to the mixer.
3. Weigh Belt Feeders: Weigh belt feeders combine the functionality of a belt feeder with the ability to accurately measure the mass flow rate of the material being delivered. This allows for precise control and monitoring of the feed rates, making them ideal for applications where accurate dosing is critical.
4. Vibratory Feeders: Vibratory feeders are designed to handle materials with cohesive or sticky properties, providing a reliable and consistent flow of material to the processing equipment.
Each type of feeding system has its own set of advantages and considerations, and the selection of the most suitable system depends on factors such as the characteristics of the raw materials, production requirements, and budget constraints.
Benefits of a Well-Designed Feeding System
A well-designed feeding system offers several benefits that directly contribute to the efficiency and quality of gypsum board production. Some of these benefits include:
1. Improved Process Control: A reliable feeding system ensures precise control over the composition of the gypsum slurry, leading to consistent board quality and performance.
2. Enhanced Efficiency: By delivering the raw materials in a controlled and consistent manner, a well-designed feeding system minimizes material waste and reduces the risk of production bottlenecks.
3. Quality Assurance: Consistent and accurate feeding of raw materials is essential for ensuring the quality and performance of the finished gypsum boards, meeting the required specifications and standards.
4. Reduced Downtime: A reliable feeding system minimizes the risk of equipment breakdowns and production interruptions, leading to improved overall equipment effectiveness (OEE) and reduced maintenance costs.
5. Flexibility and Adaptability: A well-designed feeding system can easily adapt to changes in production requirements, allowing for seamless adjustments to feed rates and material proportions.
In summary, the feeding system is a key component of the gypsum board production line and plays a key role in ensuring an efficient and consistent supply of raw materials during the production process. Our well-designed feeding systems offer many benefits, including improved process control, increased efficiency and quality assurance. Whether you are a contractor, builder or dealer, our gypsum board production line provides a reliable and cost-effective solution for sourcing quality gypsum board for your construction project. With a focus on precision, efficiency and sustainability, our production lines set new standards for gypsum board manufacturing in the industry. Experience the difference with our advanced drywall production line and enhance your building projects with quality gypsum board.
Post time: Jul-09-2024