Gypsum Powder Production Line Design
Gypsum powder is one of the five major cementitious materials, processed through crushing, grinding and other processes, widely used in construction, building materials, industrial molds and art models, chemical industry and agriculture, food processing, medicine and beauty and other applications, is an important industrial raw material.
Gypsum Powder Machinery Gypsum stone is crushed into particles smaller than 25 mm using a crusher. It is stored in a raw material silo and then conveyed to a grinding mill to make gypsum powder. The powder is sorted through a classifier. Qualified powders that meet the required fineness should be sent to the calciner, while unqualified powders should be returned to the mill for further processing. Calcined gypsum powder (usually called cooked gypsum) shall be stored in the finished silo to prepare raw material for gypsum board.
The Value of Gypsum Powders
Gypsum powders can be used in interior wall and ceiling surfaces, and the feature of non-combustibility that can be applied in porous concrete blocks. The gypsum powders produced by gypsum grinding mill with whiteness over 97%, end product fineness range from 75-44μm, which can be directly used on internal backgrounds such as concrete walls, block, brick, etc. Once settled, the gypsum would not expand or shrink, and without shrinkage cracks.
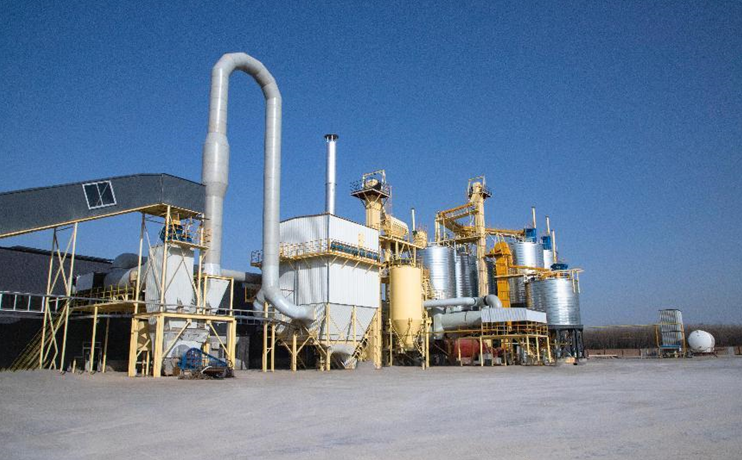
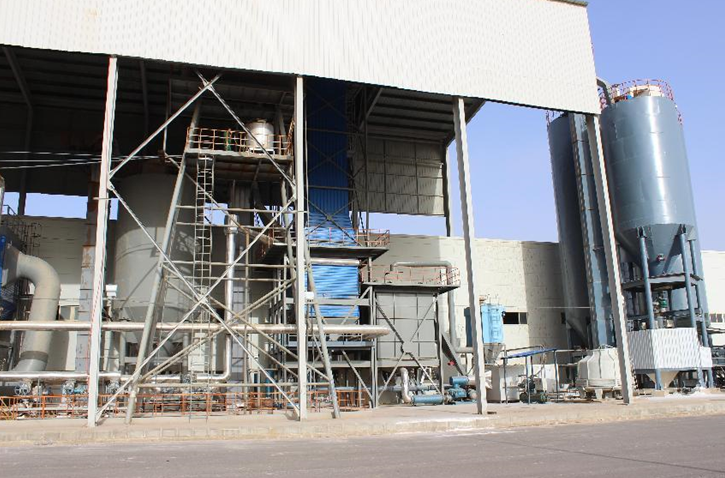
Gypsum powder production process
Step 1. Crushing system
Gypsum ore mining after particle size, specifications vary, according to the actual situation to choose the applicable crushing equipment for preliminary crushing processing, crushing the particle size of not more than 35mm.
Step 2. Storage and transportation system
The crushed gypsum raw materials are transported to the storage silo by elevator, the storage silo is designed according to the requirement of material storage time to ensure the stable supply of materials, at the same time, the elevator is used in all parts of the material turnover to reduce the floor space.
Step 3. grinding system
Grinding process is the core process of gypsum powder production, the gypsum raw materials in the storage silo through the vibrating feeder into the mill for fine grinding, electromagnetic vibrating feeder is set below the storage silo, interlocked with the mill, according to the operating conditions of the mill to adjust the supply of materials in a timely manner.
The materials are evenly and continuously fed into the mill for grinding by the electromagnetic vibrating feeder.
The crushed gypsum powder is blown out by the airflow of the mill blower, and classified by the analyzer above the main machine, and the powder that meets the specification fineness enters into the large cyclone collector with the airflow, and is discharged through the discharge pipe after collection, which is the finished product.
Finished products fall into the screw conveyor, transported to the next level of the system for calcination. Airflow from the cyclone collector back to the blower, the entire wind system is a closed loop, flowing under negative pressure. As the milled raw materials contain moisture, which evaporates into gas during the milling process, resulting in an increase in the airflow in the circulating air circuit, the increased airflow is introduced into the bag filter from the pipe between the large cyclone collector and the blower, and then discharged into the environment to ensure a clean environment.
The particle size of the material through the grinding system changes from 0-30mm to 80-120 mesh, which meets the requirement of the fineness of gypsum powder.
Step 4. Calcine system
After grinding, the finely ground gypsum powder is sent to rotary kiln for calcination by the powder selector, the cooked gypsum is sent to storage by the elevator, and the materials that do not meet the requirements continue to return to the mill for grinding; the system mainly includes elevator, boiling furnace, electrostatic precipitator, Roots blower and other equipment
Step 5. Electrical control system
The electrical control system adopts the current advanced centralized control, DCS control or PLC control.
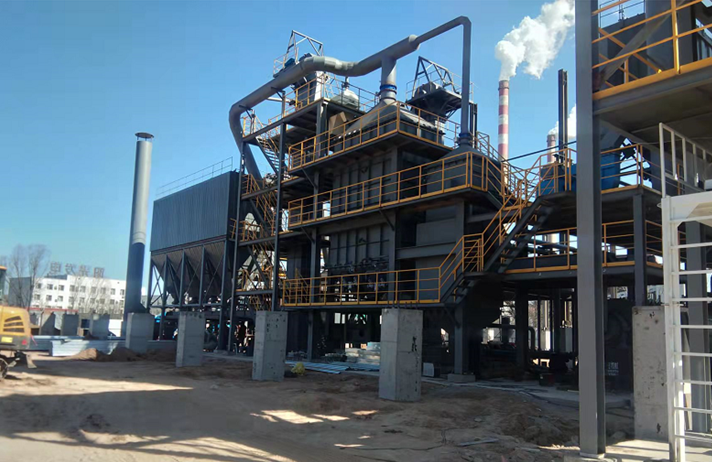
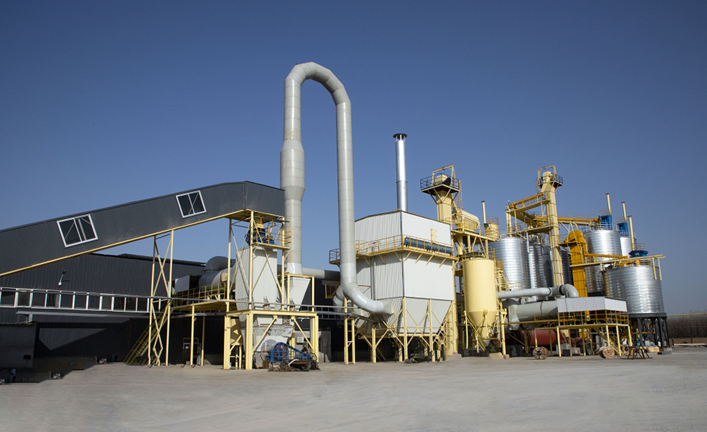
Our Gypsum Powder Production Line
{Model}: Vertical Mill
{Intermediate diameter of milling dial}: 800-5600mm
{Feeding material moisture}: ≤15%
{Feeding particle size}: 50mm
{End product Fineness}: 200-325 mesh (75-44μm)
{Yield}: 5-700t/h
{Applicable industries}: Electricity, metallurgy, rubber, coatings, plastics, pigments, inks, building materials, medicine, food, and so on.
{Application materials}: carbide slag, lignite, chalk, cement clinker, cement raw material, quartz sand, steel slag, slag, pyrophyllite, iron ore and other non-metallic minerals.
{Grinding characteristics}: This Gypsum Powder Production Line has a very strong adaptability to soft, hard, high humidity, and dry materials and with diverse applications. High grinding efficiency resulting in higher yield in less time.
If you are ready to take your business to the next level with a top-notch gypsum powder production line, please do not hesitate to contact us. Our knowledgeable team is ready to assist you and provide all the information you need to make an informed decision. We are confident that our gypsum powder production lines will exceed your expectations and contribute to the success of your business. Get in touch with us today to learn more about our products and services.
Post time: Aug-10-2024